Aluminum is a lightweight, strong and flexible metal that resists corrosion and is 100 per cent recyclable. It is a common material in vehicles, buildings, consumer goods, packaging, power transmission and electronics. Canada’s aluminum industry began at the turn of the 20th century and grew quickly during both World Wars. In 2022, Canada produced approximately 3.0 million tonnes of primary aluminum, making it the world's fourth largest primary aluminum producer. The country nevertheless accounts for 4.4 per cent of global production. Aside from one smelter in Kitimat, British Columbia, all Canadian plants are in the province of Quebec.
Click here for definitions of key terms used in this article.
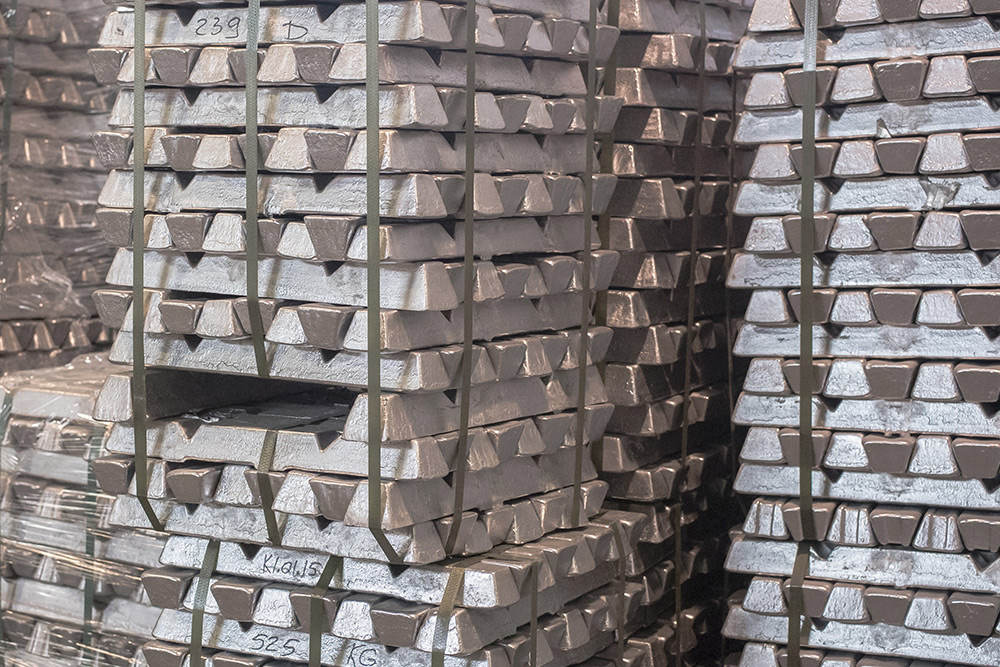
What Is Aluminum?
Pure aluminum (Al) is a silver-white, malleable metal capable of being drawn out into wire. It has one-third the density of steel. Aluminum is the most abundant metallic element in the Earth’s crust. Unlike most of the other major metals, aluminum does not occur in its native (chemically uncombined) state. Rather, it is widespread in the environment as silicates, oxides and hydroxides, in combination with other elements such as sodium and fluoride, and as complexes with organic matter. When combined with water and other trace elements, it produces the main ore of aluminum known as bauxite. Aluminum’s dull sheen results from a thin coating of oxygen that forms when it is exposed to air. This feature accounts for the metal’s resistance to corrosion. Aluminum is an excellent conductor of electricity. It has twice the electrical conductance of copper. It is also an efficient conductor of heat and a good reflector of light and radiant heat.
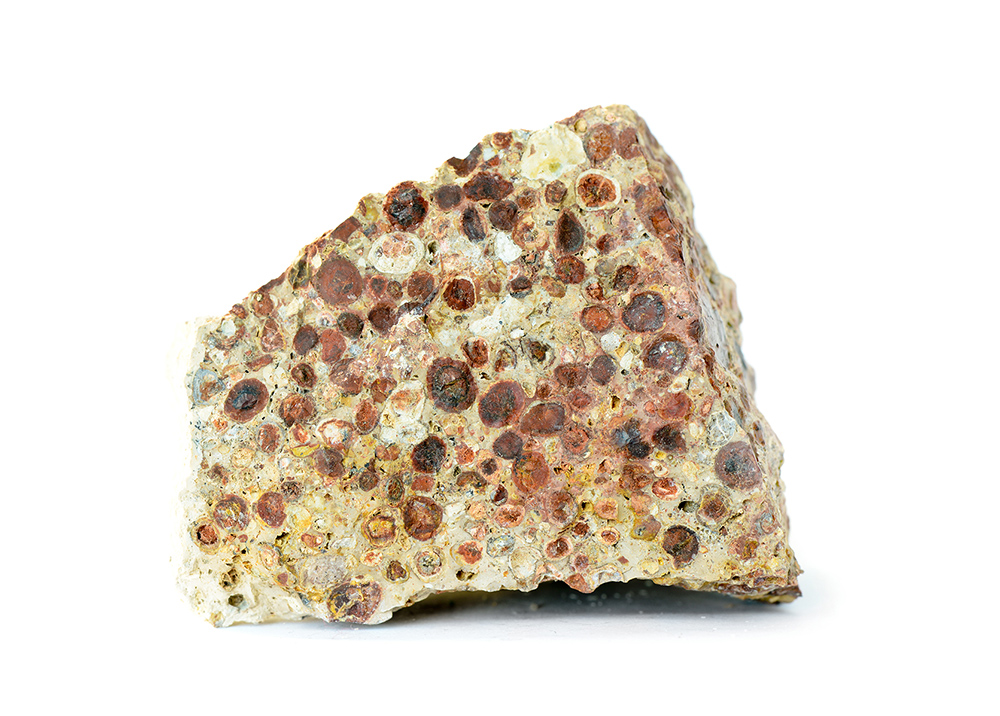
Origins of the Aluminum Industry
Danish scientist Hans Christian Oersted first isolated aluminum metal in 1825. For the next 60 years, though, there was no economical way to produce the metal commercially. That changed with the independent discoveries of Charles M. Hall of the US and Paul-Louis Toussaint Héroult of France in 1886. Hall and Héroult found a way to extract aluminum from alumina (aluminum oxide). The next year, Austrian engineer Karl Josef Bayer developed a process to extract alumina from bauxite ore. The world aluminum industry is still based on the Hall-Héroult and Bayer methods. (See How Is Aluminum Made?)
Another key development came from German metallurgist Alfred Wilm’s experiments with age hardening. Wilm revealed that leaving aluminum alloys to cool slowly (rather than “quenching” them quickly) produced a much stronger — but still lightweight — material. Age-hardened aluminum alloys revolutionized technology in the 20th century. They became crucial materials in transportation (e.g., automobiles, rail cars and planes), electric utilities (e.g., power lines) and tall buildings.
Did you know?
There are two current spellings the metal’s name: aluminum and aluminium. North Americans tend to write and say aluminum (“al-u-mi-num”). In the rest of the English-speaking world, aluminium (“al-u-mi-nee-um”) is common. Neither name is the one that English chemist Sir Humphry Davy first gave the element in 1807. He originally called it alumium (“al-u-mee-um”). A few years later, though, he started using the term aluminum. That spelling stuck in North America. The other countries retained the -ium ending, echoing the names of other elements such as potassium and sodium.
How Is Aluminum Made?
Bauxite is the main ore of aluminum. It contains about 40-60 per cent alumina (aluminum oxide, Al2O3), as well as silica and iron oxide. Bauxite is formed by the weathering of aluminum-rich rocks under tropical conditions. There are no bauxite mines in Canada. The country’s refinery and smelters use ore and refined alumina imported from other countries. In 2022, imports of bauxite and alumina accounted for $2.2 billion of Canada’s aluminum imports. (See also Imports to Canada.)
Aluminum is produced by separating pure alumina from bauxite in a refinery, then treating the alumina by electrolysis. An electric current flowing through a molten electrolyte, in which alumina has been dissolved, separates the aluminum oxide into oxygen and aluminum metal. In this process, the oxygen collects on carbon anodes immersed in the electrolyte. The aluminum metal collects on the bottom of the carbon-lined cell (cathode). On average, it takes about four tonnes of bauxite to obtain two tonnes of aluminum oxide, which in turn yield one tonne of metal. Smelters produce uniform bars of aluminum called ingots. These are shipped to manufacturers to be shaped into specific products.
Aluminum Alloys
Combining aluminum with other metals to produce alloys enhances its properties and makes it more versatile. The most common metals combined with aluminum are copper, magnesium, manganese, silicon and zinc. Aluminum’s tensile strength (resistance to breaking under tension), hardness, corrosion resistance and heat-treatment properties improve when alloyed with one or more of these metals. Some copper-aluminum alloys, for example, can exceed the tensile strength of mild steel by as much as 50 per cent.
In both its pure and alloyed forms, aluminum is used to make a variety of consumer goods and capital goods (materials for making other goods). The largest markets for aluminum are transportation, construction, consumer goods, packaging, electrical and machinery/equipment. China is the largest consuming region, followed by North America and the rest of Asia.
History of Aluminum Production in Canada
Aluminum production uses large amounts of electricity. For this reason, the Canadian industry took root in Quebec, where renewable hydroelectric energy could be harnessed at low cost. The rivers that run off the Canadian Shield into the St. Lawrence Lowland give the province its hydroelectric potential.
In 1901, the Northern Aluminum Company (later named Alcan) opened a smelter powered by a hydroelectric plant on the Saint-Maurice River in Shawinigan. This company was a Canadian subsidiary of the Pittsburgh Reduction Company owned by the same Charles M. Hall of the Hall-Héroult process.
During the First World War, global production of aluminum nearly doubled due to demand from weapons and aircraft manufacturers. There was a particular need for aluminum powder, a key ingredient in explosives. The Shawinigan plant increased its output to meet demand.
A second smelter began operations in 1926 in Arvida. Arvida was a company town designed and built by the Northern Aluminum Co. for the smelter’s workforce. An alumina refinery opened there in 1928.
With the outbreak of the Second World War in 1939, demand for aluminum surged once again. Global production almost tripled. Aluminum alloys were used in the frames of hundreds of thousands of new war planes. Canada’s production of the metal grew from 68,000 tonnes in 1939 to more than 400,000 tonnes in 1943. The plants in the Saguenay region produced 40 per cent of the aluminum that the Allies used during the war. Alcan built another smelter in Shawinigan in 1941, and one in each Beauharnois and La Tuque the next year.
Did you know?
During the Second World War, thousands of workers at the Arvida plant staged an illegal strike. They demanded better pay and working conditions. After the workers occupied the plant, the federal minister of Munitions and Supply, C.D. Howe, told the press he suspected enemy sabotage. Two companies of soldiers were sent to protect the factory. However, a royal commission later rejected the sabotage theory. (See Arvida Strike.)
Demand for aluminum dropped briefly after the Second World War. The market was still flooded with the metal from wartime production. However, the use of aluminum for nonmilitary purposes grew in the postwar years. Aluminum became more common in the automotive, aerospace and household-products industries. In 1951, Alcan began building a smelter in Kitimat, British Columbia. This was the first — and remains the only — smelter outside the province of Quebec.
Alcan’s first domestic competitor was the Canadian British Aluminum Company. It emerged in the 1950s, establishing a smelter in Baie-Comeau, Quebec. The Canadian Reynolds Metals Company later bought the smelter and expanded it in 1985 and 1991. Until 1986, Alcan and Canadian Reynolds were the only primary aluminum producers in Canada. Within several years, three more companies had joined the market with plants in Quebec: Aluminerie de Bécancour Inc. (1987), Aluminerie Lauralco Inc. (1992) and Aluminerie Alouette Inc. (1992). Total production capacity in Canada was 2.3 million tonnes per year. This capacity was higher than the world production of aluminum during the Second World War.
The Canadian Aluminum Industry Today
Canada’s aluminum industry continues to draw on the abundance of hydroelectric power at competitive prices, a qualified labour force and modern public infrastructure (e.g. roads and railways) close to major markets. However, it has been shrinking over the last two decades. In 2018, the Canadian aluminum industry employed more than 8,700 people, compared to more than 14,000 in 2003. Competition from China, India and the Middle East is one cause of this trend, as is the increased use of secondary (recycled) aluminum.
Canada currently produces primary (as opposed to recycled) aluminum at eight smelters in Quebec and one in Kitimat, British Columbia. Each plant belongs to one of three companies: Alcoa, Aluminerie Alouette and Rio Tinto (which bought Alcan in 2007). Rio Tinto also has an alumina refinery in Vaudreuil, Quebec. Canadian manufacturers of aluminum products make items such as doors, windows, house siding, beverage cans, foil products, cooking utensils and electrical wiring.
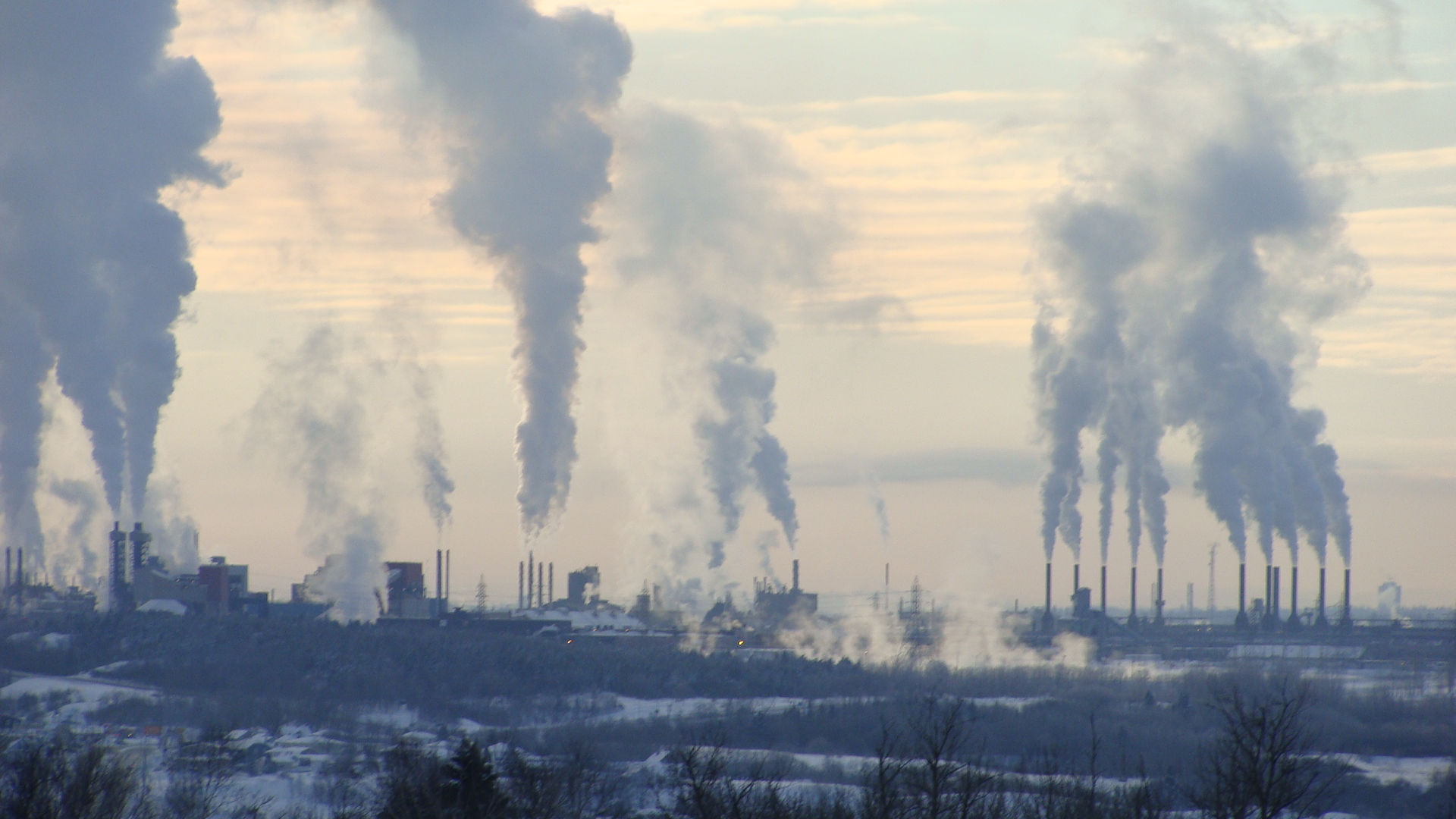
As of 2022, Canada was the world’s fourth largest producer of primary aluminum, after China, India and Russia. In 2022, Canada produced an estimated 3.0 million tonnes of primary aluminum. However, Canada’s output represents only about 4.4 per cent of global production. China alone makes more than half of the world’s aluminum. Canada’s carbon footprint from aluminum production is lower than that of other countries that are major producers. This owes to the Canadian industry’s use of renewable energy (see Hydroelectricity).
Canada is the world’s second largest exporter of aluminum. Exports of aluminum products from Canada were worth $18.2 billion in 2022. The United States is the most important market for Canadian exports of aluminum products.
Secondary (Recycled) Aluminum
Secondary aluminum production continues to increase worldwide. Improvements in scrap collection systems and increased recycling rates have contributed to this growth. Recycling aluminum requires 5–8 per cent of the energy used to make the original metal. The process is also cheaper and quicker. The automotive industry is a major consumer of secondary aluminum. Demand for secondary aluminum has grown as automakers produce lighter, more fuel-efficient vehicles.
See also Metallurgy.