Iron is the primary raw material used to produce steel — itself an alloy of concentrated iron with a minute amount of carbon. (See also Mineral Resources in Canada.) Globally, steel production drives 98 per cent of the demand for iron, while electronics and non-metallurgical uses drive the remaining 2 per cent. Iron extraction and steel production have historically constituted major industries in Canada, especially in the industrial zones of Ontario and Quebec.
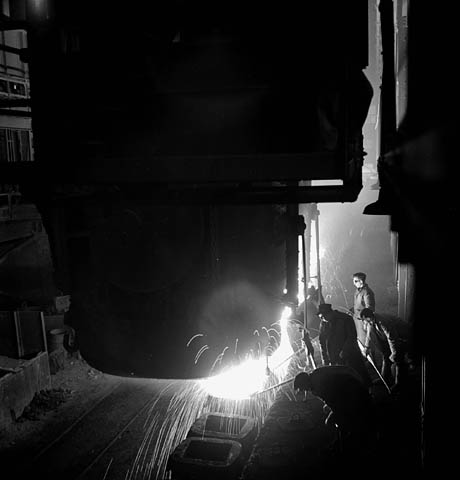
Iron Ore
After oxygen, silicon and aluminum, iron is the fourth most plentiful element in Earth's crust. It occurs in certain minerals, the most important being magnetite, hematite, goethite, pyrrhotite, siderite, ilmenite and pyrite. The term "iron ore" is used when rock is sufficiently rich in iron minerals to be mined economically. Pyrite and pyrrhotite, although plentiful, are rarely used as iron ores because of the high amounts of sulphur they contain. Canadian iron ores consist mostly of hematite or magnetite, and some siderite and ilmenite. Besides oxides of iron, iron ores contain gangue — minerals such as quartz or fluorite not wanted in iron making.
Ores containing proportions of iron of 54 per cent or more are considered high-grade, while those containing lower proportions of iron must be upgraded in order to become technically marketable as iron ore. Iron-bearing rock may be upgraded by removing gangue through concentration. This requires fine grinding of the ore, followed by separation of the iron-rich from the gangue particles (e.g., through magnetic separation). The upgraded iron-rich material ("concentrate") must be agglomerated into larger lumps prior to smelting, either by tumbling it into pellets ("pelletizing") or by heating the concentrate until its particles stick together ("sintering").
As of 2023 Canada is the world's eighth-largest producer of iron ore. The largest corporate producer is the Iron Ore Company of Canada, (of which Rio Tinto controls a majority share). Canada exported 58.2 million tonnes of iron ore in 2023, which was valued at $8.9 billion. That same year, it imported 8.2 million tonnes of iron ore, worth $1.1 billion.
Iron ore is mined in Newfoundland and Labrador, Quebec and Nunavut. By far the largest geological source of iron in Canada is the Labrador Trough, an immense formation that winds through Newfoundland and Labrador and northern Quebec. Combined, these provinces account for virtually all of the iron ore mined in Canada. First discovered in 1892, the Trough has been the site of iron extraction since 1954 and in recent years has garnered increasing attention from the extractive sector as demand for the resource has grown.
Steel
Steel is the world's most important industrial material, with over 1.89 billion tonnes of crude steel produced globally in 2023. Without steel, the world as we know it would not exist: from oil tankers to thumbtacks, from trucks to tin cans, from transmission towers to toasters. Given the huge quantities of steel produced, it is fortunate that the material is easy to recycle. In fact, many of Canada's steel plants make steel totally from scrap. In 2023, Canada exported 4.8 million tonnes of steel scrap.
Despite Canada’s formidable reserves of iron ore, the steel industry in recent decades has shrunk significantly as industrial markets have become increasingly globalized. Today, every remaining steel mill in the country is owned by foreign investors and Canada is a net importer of the manufactured product. In 2023, Canada imported 8.4 million tonnes of semi-finished steel products and exported 6.6 million tonnes.
Iron and Steel Production
Iron production requires iron ore, coal and stone (limestone, dolomite). Steel production requires iron, steel scrap and flux ("lime" — calcined limestone). The iron ore is smelted to produce an impure metal called "hot metal" when liquid, or "pig iron" when solid. The hot metal is refined to remove impurities and to develop the desired composition. The liquid steel is continuously cast into blooms, slabs or billets, and these semi-finished products are processed into the desired shapes by rolling or forging.
Industry Components
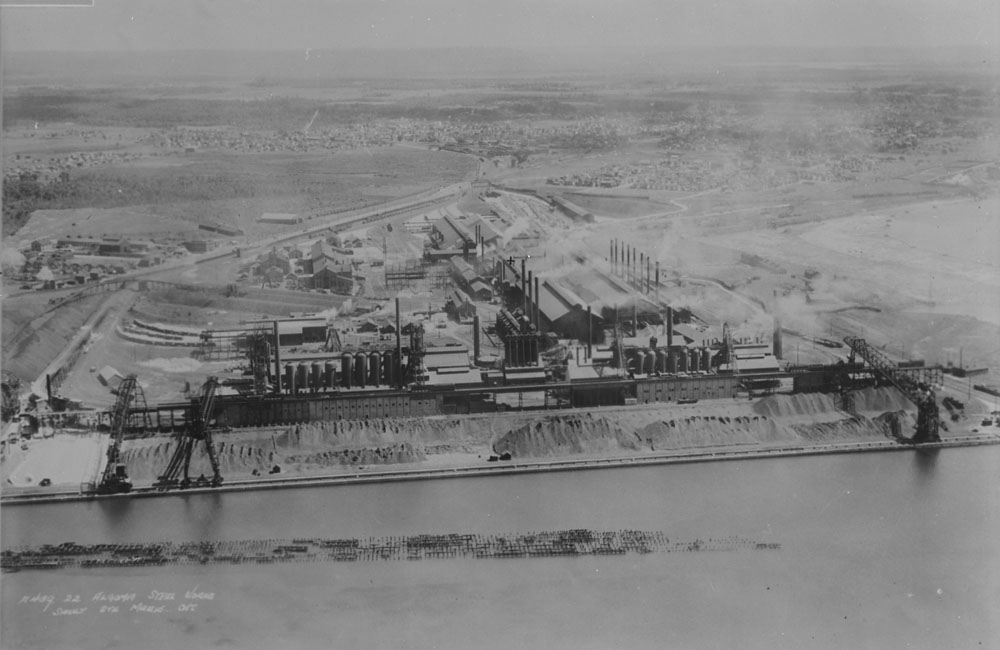
The iron and steel industry is divided into four groups: iron and steel integrated producers; steel integrated companies; steel processors; and foundries and fabricators.
Iron and Steel Integrated Producers
Iron and steel integrated producers (ore-based) are typically large firms that operate ore and coal mines (frequently as joint ventures), as well as iron and steelmaking plants. Producers include such companies as Algoma Steel of Sault Ste. Marie, Ontario, ArcelorMittal Dofasco of Hamilton, Ontario, and ArcelorMittal of Montreal (formerly Sidbec-Dosco).
Integrated Steel Producers
Integrated steel producers depend on scrap as their source of iron. They can make the same range of semi-finished (slabs, blooms and billets) and finished steel products as the larger iron and steel integrated producers (hot- and cold-roll strip, plate, rod, bars, shapes). Producers include such companies as Gerdau-AmeriSteel of Whitby, Ontario, and ArcelorMittal in Contrecoeur, Quebec.
Integrated steel plants are located wherever it is economically feasible to bring together large quantities of the raw materials required. The biggest steel plants in Canada have been built along the Great Lakes and St. Lawrence Seaway system, where they receive iron ores from northern Ontario, Quebec, Labrador, Minnesota, Wisconsin and Michigan, and coal from Pennsylvania, West Virginia and Kentucky. Other integrated steel plants, however, have been built in areas where abundant scrap and a ready market for finished steel exists.
Steel Processors
Steel processors purchase semi-finished and hot- and cold-rolled steel products from the integrated companies and custom process them for resale to fabricators wanting steel quantities too small for the integrated companies to handle economically. Scrap recycling companies are included in this group. Processors include such companies as DJ Galvanizing Corporation of Windsor, Ontario, for hot dip galvanizing, and Union Drawn Steel of Hamilton, Ontario, for bar drawing.
Foundries and Fabricators
Foundries, often small, produce various grades of cast iron and/or steel. The molten metal is ladled or poured into sand or metal moulds. The cast parts produced can be complex in shape, and often designed to meet one-of-a-kind end uses. Fabricators take the various primary steel mill products and turn them — cut-to-size, shape, machine, thread, punch, join, protective coat, etc. — into a host of commercial and industrial products. Foundries and fabricators include such companies as Baycoat Ltd. of Stoney Creek, Ontario, for organic coating, and Bombardier Inc. of Valcourt, Quebec, for stamping and welding.
Iron Making
When iron is being made ore, coke and stone are introduced through the top of the blast furnace at regular intervals. (Coke is the partially graphitized solid residue left after the volatile components of bituminous coal are removed by heating in coke ovens.) As they slowly descend down the furnace shaft, these materials ("burden") are heated by rising hot gases. The carbon monoxide in these gases reacts with the iron oxides in the ore to form metallic iron and carbon dioxide. The iron formed melts and, as it percolates through the coke column, dissolves carbon. By the time it reaches the hearth, it is saturated with carbon, and it also contains silicon, phosphorus, manganese and sulphur. The stone and ore form a low-melting, free-running liquid slag, which absorbs most of the sulphur entering the furnace (coke is the main sulphur source). Liquid slag, composed of gangue minerals and oxide components of stone, floats on the liquid iron and is separated from the molten metal during furnace tapping. The coke does not melt; it burns on contact with the pressured, preheated air ("blast") entering through the tuyères located just above the hearth.
Direct Reduction
Several solid-state reduction processes have been developed in which iron ore is converted to metallic iron without melting. Because there is no separation of iron from gangue in the reduction facility, high-grade ores or concentrates (>90 per cent iron) must be used. Many of these solid-state processes use natural gas as the fuel and as the reducing agent (carbon monoxide and hydrogen). ArcelorMittal operates such a process, known as the Midrex Process, at Contrecoeur, Quebec.
Solid-state reduced ore and/or pellets, known as DRI (Direct Reduced Iron), are melted in electric arc furnaces and converted to steel in the same way as scrap metal. During the steelmaking process, the gangue in DRI is removed; the gangue minerals contained in DRI combine with the added lime to form a fluid slag. DRI is superior to scrap in purity and uniformity of composition but these benefits come at a higher cost.
Steelmaking
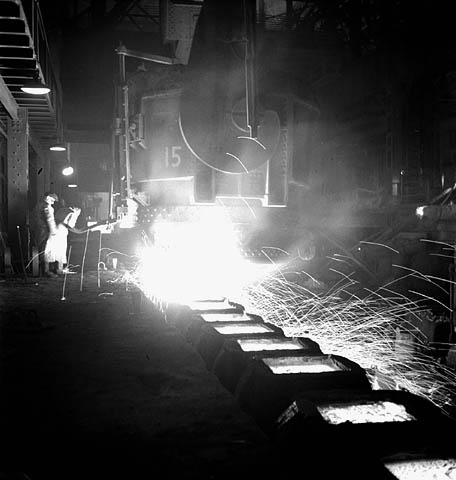
Steel is an alloy of pure iron and carbon in which the carbon content varies from about 0.002 per cent (e.g., deep-drawing sheet metal) to 1.5 per cent (e.g., tool steels). Alloy steels contain additional elements (such as manganese, nickel, chromium, vanadium, molybdenum) that give them greater strength and specific properties. Stainless steel, for instance, is an alloy of chromium and nickel. In addition to carbon, hot metal and pig iron may contain unwanted elements such as silicon, phosphorus and sulphur. During the steelmaking process, these elements, which make steel brittle, must be removed.
In the process of steelmaking, the hot metal, along with some scrap, is fed into a refractory-lined vessel ("converter"). Oxygen gas is then injected into the bath of hot metal. Also, lime is added to produce a slag that dissolves sulphur and other unwanted impurities, but does not corrode the converter lining. The injected oxygen gas oxidizes the carbon dissolved in the hot metal to form carbon monoxide and generate heat. When the carbon content of the molten bath drops to the desired level, alloying elements are added, and the liquid steel is tapped into a preheated ladle.
Scrap-based steel producers use electric arc furnaces. The scrap is charged into the furnace and three graphite electrodes descend through the furnace roof. As the electrodes approach the scrap, arcs form (high-voltage power). Due to its higher electrical resistance and to the intense heat radiated by these arcs, the scrap quickly heats to melting temperatures.
Ladle Refining
The liquid steel destined for demanding applications is further refined in ladle treatment units. The remaining impurities, such as sulphur, hydrogen, nitrogen, and non-metallic inclusions, are removed. The methods used include argon stirring, powder desulphurization, and vacuum degassing.
Continuous Casting
Some years ago, the majority of steel was cast into ingots. Ingots are large, rectangular blocks of steel, most of which are subsequently shaped into semi-finished products — blooms, slabs, billets or special shapes — by primary rolling or forging. Today, continuous casting (CC) is the principal way to solidify and shape liquid steel into semi-finished products. CC eliminates the primary operations. In the CC machine, liquid steel is poured into the top of a water-cooled, oscillating copper mould, and the slab, bloom or billet is discharged continuously from the bottom. In recent years, thin slab casting has gained favour as it eliminates several production steps.
Hot and Cold Rolling
For the most part, slabs, blooms and billets are reduced in rolling mills to hot- and cold-rolled products such as plate, strip, rail, structural shapes, bar and wire rod. Some steels (e.g., sheet, strip) are finished by cold rolling at room temperature to obtain close dimensional tolerances, high-quality surface finish and an exact degree of hardness.
Heat Treatment
Heat treatments include annealing, normalizing, quenching, and tempering. These treatments change the properties of steel by altering its crystalline microstructure.
Protective Coatings
When subjected to certain environments, steel corrodes. To slow the oxidation of steel (rusting) steel products are coated. The most common coatings include zinc, tin, aluminium, vitreous-enamel and organic coatings (e.g., paint).
History of Iron and Steel Production in Canada
In Canada, the Forges Saint-Maurice, near Trois-Rivières, Quebec, produced iron from local bog iron ore and charcoal to supply settlers and the military (see Blacksmithing). The first ironworks in Upper Canada, the Marmora Ironworks, near Peterborough, Ontario, began production in 1822. It consisted of two charcoal-fired blast furnaces, a forge with two sets of water-powered hammers and special hearths for the production of iron bar. In the late 19th century both the Marmora and the Saint-Maurice ironworks were closed; they could no longer compete with more modern ironworks in Ontario and Nova Scotia, which employed coke-fired blast furnaces.
Steel products were first manufactured in Canada in the 1880s. By the early 1900s steelmaking centres had been established in Hamilton and Sault Ste. Marie, Ontario, and in Sydney, Nova Scotia. Iron and steel production grew slowly until the Second World War and then rapidly as the postwar economic boom created a tremendous demand for steel.
The Bessemer Process, invented in England in 1856, was the first large-scale steelmaking process. This method was followed by the invention, a few years later, of the open-hearth process, which from about 1900 to the early 1960s accounted for most of the steel production in the world. By 1910 the Bessemer Process was no longer in use in North America.
The Basic Oxygen Process (BOP) — known first as the LD Process — originated in Austria. Dofasco Inc introduced the BOP to North America in 1954 and since then the dominant open-hearth process steadily declined, and none are in use today.
Canadians have made notable contributions to the advancement of the iron and steel industry. In the early 1960s Canadian Liquid Air designed an injector that made it possible to introduce pure oxygen through the bottom of BOP vessels. This method was developed to industrial scale in Germany in 1968. The first successful continuous casting machine for steel in North America was developed by Atlas Steels, Welland, Ontario, in 1954.
In 1959, Stelco Inc introduced low slag volume blast furnace practice that decreased coke consumption by about 40 per cent, saving the world over 200 million tonnes of coal a year. Stelco developed the Stelmor rod cooling process, and the Coilbox, a major energy-saving device used in hot-strip rolling mills. Also, it developed the short annealing cycle, another energy-saving development, universally adopted by the steel industry. And Stelco developed the Ardox spiral nail. Lasco developed a slit-rolling technique to make two bars from a single billet. Ipsco was the first company to install a spiral-weld pipe mill.
Projet Bessemer Inc., a consortium of Canadian steel producers and the National Research Council of Canada, has undertaken research into strip casting at Boucherville, Quebec — the ultimate goal in steelmaking: one step from liquid steel to finished strip.